Intelligent high-pressure ball press
Keyword:
Classification:
Product Details
Product Introduction
High-pressure briquetting machine is a device that presses various dry and wet powder materials into briquettes with higher bulk density through a pre-pressing device and into the roll pressing area. It is used to press fully mixed materials into pellets. This equipment is used to press aluminum ash into balls and can also be used to press aluminum ash mixed with other powdery materials into balls. It is mainly used in the light metal industry, such as coal, mining, metallurgy, refractory materials, and building materials.
Our company's independently developed energy-saving, environmentally friendly, and intelligent high-pressure briquetting machine is a high-quality equipment developed based on the principle of extrusion molding of powdery materials. It consists of two counter-rotating and synchronously rotating extrusion rollers, both roller surfaces are processed with concave pits of a certain shape. Fine powder and small particles are fed from above the two rollers and into the engaging angle between the two extrusion rollers. Under the action of the driving force of the two rollers and the high-pressure extrusion force provided by the hydraulic system in the horizontal direction of the two rollers, the material is forcefully squeezed into the concave pits on the surface of the two rollers for compaction and molding. Then, as the two rollers rotate downwards, they are released due to gravity and the elasticity of the material itself.
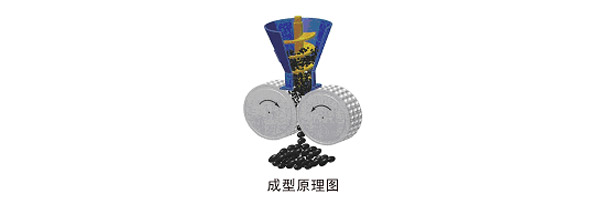
The JNHB intelligent high-pressure briquetting machine is widely used in the mining, coal, metallurgical, pharmaceutical, and chemical industries for materials such as coal powder, iron concentrate, metal shavings, various slags and mineral powders, metallurgical sludge, coal sludge, magnesium metal raw materials, and refractory materials. It has the advantages of small footprint, high efficiency, no pollution, low energy consumption, and strong practicality. The company has a high-pressure molding testing machine with a line pressure of 300KN/cm, which can conduct pellet experiments for customers.
Product Advantages and Features
Compared with products from German companies and similar domestic products, this product has significantly advanced performance.
1. High Energy Saving: Significant energy-saving effect, the power consumption per ton is half that of ordinary briquetting machines, and the equipment weight is two-thirds that of equipment of the same specification.
2. High Environmental Protection: The molded pellets have high compressive strength, up to 1300N, and good impact and compression resistance. During storage and especially transportation, they no longer cause serious environmental pollution.
3. High Intelligence: Fully automated operation, reducing labor costs, and providing users with convenient remote services.
4. High Pressure: Line pressure can reach 300KN/cm, which is currently the highest line pressure among domestic briquetting machines, solving the problem of difficult molding of materials without adding any additives. Compared with products from German companies and similar domestic products, this product has significantly advanced performance.
①Good material extrusion effect, high balling rate, and high ball strength;
②Good roller surface performance and long service life;
③Double output shaft reducer structure is adopted to improve the accuracy of the rollers, and hard-faced gears are used to improve the performance and service life of the reducer;
④The pre-press is driven by a speed-regulating motor, and all wear parts are welded with wear-resistant alloys to improve performance and service life;
⑤The hydraulic station is placed independently, and the pressure can be adjusted with overpressure protection function.
Luoyang Zhongyuan Mining Machinery Manufacturing Co., Ltd. has formed a factory integrating development, research, testing, design, manufacturing, and service in the development of briquetting machines, and is equipped with a complete briquetting testing machine and a corresponding laboratory. Our factory can determine the process flow and process parameters through testing according to the materials used by the user, complete model selection and design and manufacturing, and is a production base with a full range of varieties and specifications and new types of briquetting machines.
Product Structure
①Feeding system: The raw materials are quantitatively fed into the rollers to ensure uniform feeding. The high-pressure briquetting machine uses a spiral feeder, driven by a speed-regulating motor, and driven by a worm gear reducer to press the raw materials into the main feed port. Due to the characteristics of the speed-regulating motor, when the pressure amount of the spiral feeder is equal to the amount of material required by the host machine, it can maintain a constant feeding pressure, thus ensuring the stability of the pellet quality.
②Transmission system: The main transmission system of the high-pressure briquetting machine includes a motor, coupling, reducer, ball trough positioning device, and coupling, respectively transmitting to the two roller shafts, their actions are opposite, and they rotate synchronously. The main power supply uses a speed-regulating motor, which is transmitted to the active shaft through pulleys and cylindrical gear reducers. Open gears are used between the driven shaft and the non-driven shaft to ensure synchronous operation.
③Molding part: This mainly refers to the main part of the machine, and its core is the roll. When there is excessive feeding or metal blocks appear, the hydraulic cylinder piston rod is overloaded, the hydraulic pump will stop, the accumulator buffers pressure changes, the overflow valve opens for oil return, and the piston rod shifts to increase the gap between the rollers, thus allowing hard objects to pass through the rollers. Such system design can protect the rollers from damage.
High-Pressure Briquetting Machine Model Catalog
Technical Parameters of Other Models
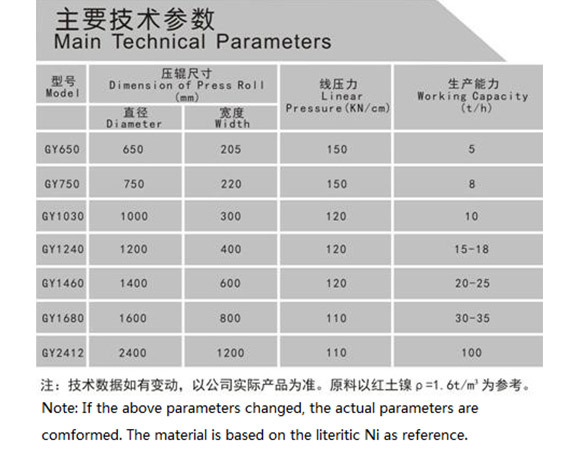
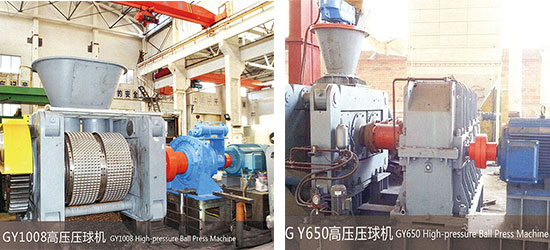
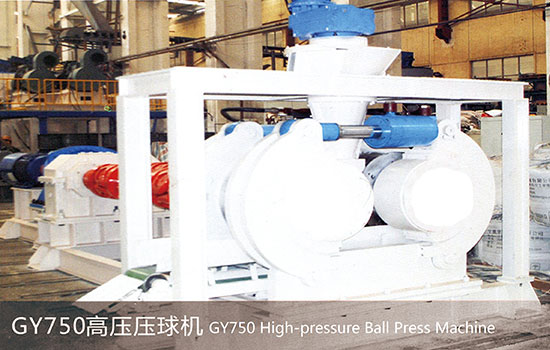
Assembly Site
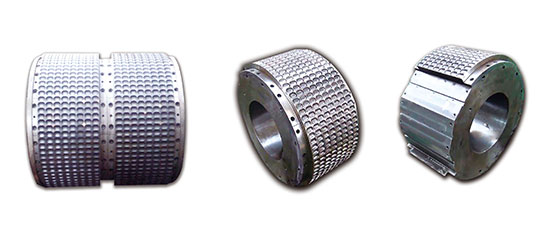
The embedded roller skin is easy to replace, and users can disassemble and replace it on site without returning it to the manufacturer. It has a long service life. The embedded roller skin has 2 to 3 times the lifespan of the whole ring set, and the cost is low.
Pressure Measurement Site
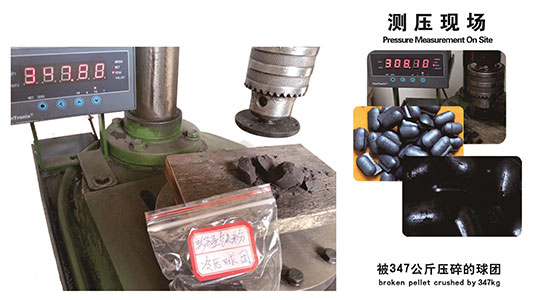
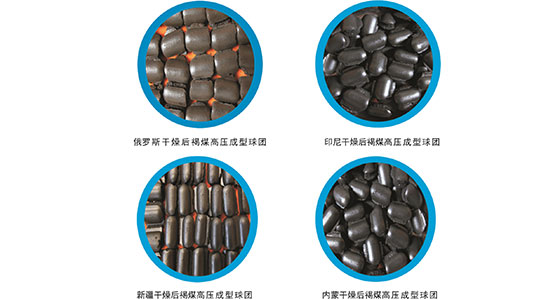
Application in Iron-Carbon Pelletizing
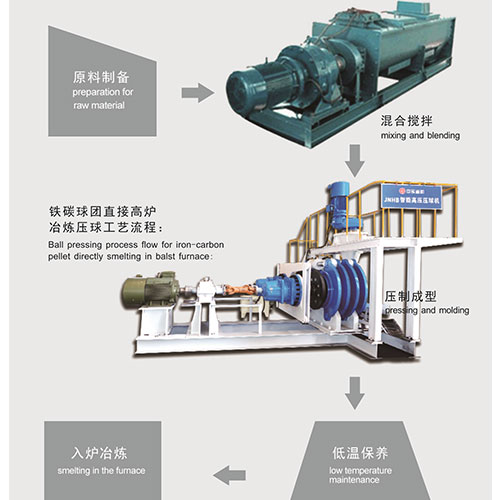
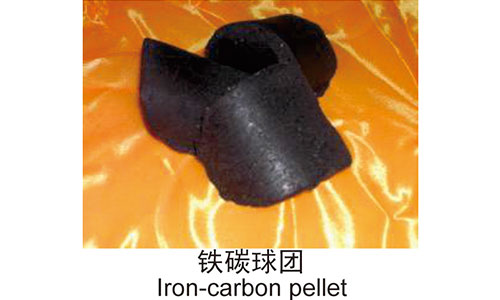
At present, blast furnace smelting generally uses sintered ore and roasted pellets for smelting. That is, iron concentrate, coke powder, bentonite, and other raw materials are mixed, granulated, and sent to a belt or disc sintering machine for high-temperature sintering, or iron concentrate powder is mixed with bentonite, disc granulated, and then sent to a vertical furnace for roasting, cooled, and then sent to a blast furnace for smelting. Both types of furnace materials require high temperatures during roasting, and heating inevitably consumes a large amount of energy, while also causing a large amount of pollution and greenhouse effects. If iron concentrate is mixed with coal powder and binder, roll-pressed granulated, and low-temperature cured to form iron-carbon pellets with high cold and hot strength and drum strength, and then directly sent to the blast furnace for smelting, it not only saves the roasting process and saves a large amount of energy and reduces the cost of blast furnace smelting, but also reduces a lot of pollution and greenhouse effects, reduces the raw material cost of the metallurgical industry, and improves profitability. On the other hand, using this new process can reduce the smelting time per furnace by half, greatly increasing the blast furnace utilization rate and ultimately improving the efficiency of enterprises.
Currently, our company's high-pressure briquetting machine, combined with a new type of binder, forms an iron-carbon pellet production line that ensures materials for blast furnace smelting. This promotes the process improvement of directly using iron-carbon pellets in blast furnace smelting. It is not only environmentally friendly and reduces consumption, increasing economic benefits, but also represents a technological revolution in blast furnace smelting in the metallurgical industry.
Applications in other fields
Briquetting machines have very wide applications in other fields, such as industrial waste, power plant waste, the magnesium metal industry, the production of gas coke, high-phosphorus oolitic hematite, and blast furnace smelting. Therefore, the advent of high-pressure briquetting machines has provided necessary conditions for improving the strength of pellets (blocks), improving production efficiency, and especially for the large-scale industrial production of pellets.
Shipping site
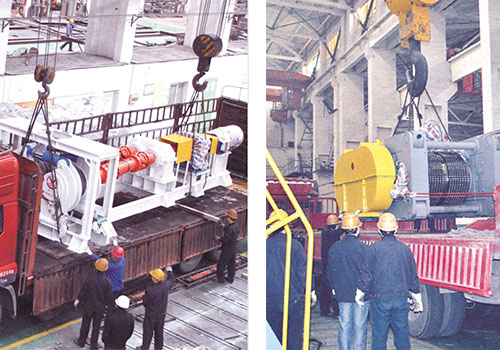
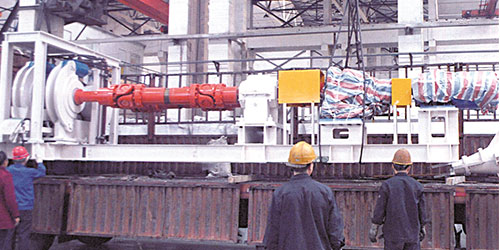
Customer site
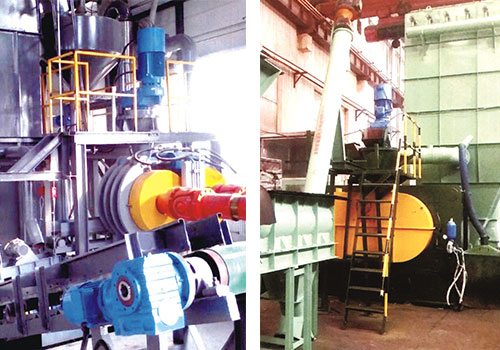
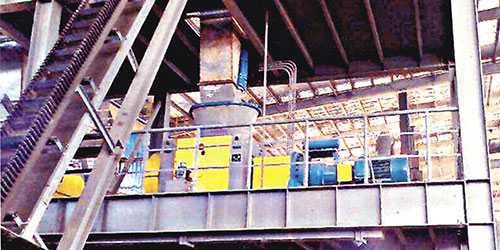
Product Query
Leave contact information and get free product quotation.
Contact Us
No.99 Hengshan Road, Jianxi District, Luoyang City, Henan Province

sweep
Luoyang Kunju
Learn more about dynamic information